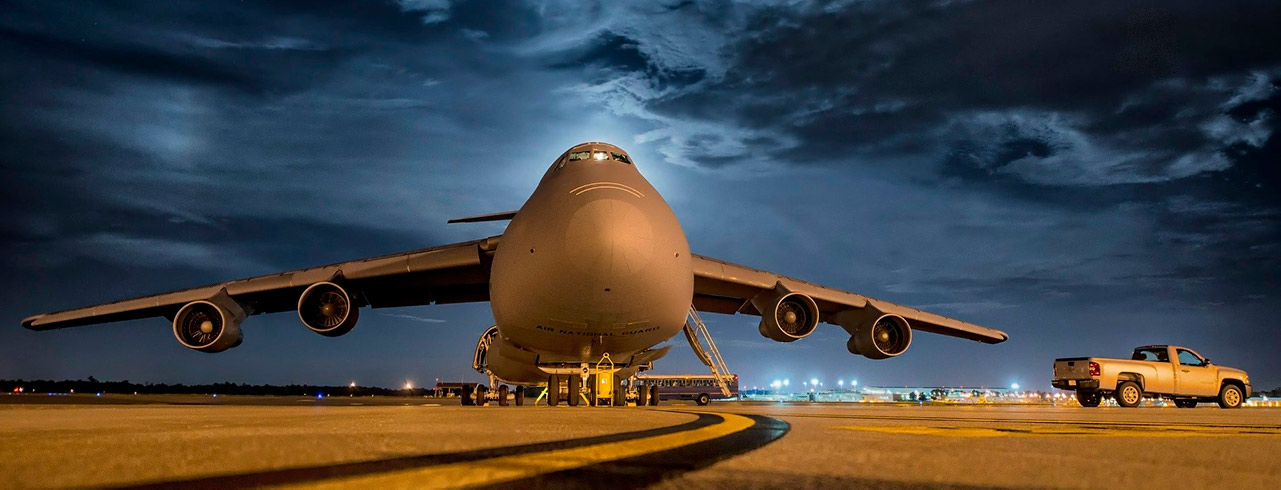
Safety has always been and will always be a primary factor in the management of any airport. With domestic and international travel constantly increasing, wear on runways and other areas of airports is greater and therefore continuously requiring constant maintenance.
Technology advances and new systems for maintenance are introduced almost daily. Restoration of safety factors, such as surface roughening and removal of rubber deposits on runways is today done without the use of chemicals which tend to damage the under laying strata. New mechanical methods also respect the concrete or asphalt while allowing for speedy interventions. Being notoriously costly, down time in airports is an element of utmost importance. With dry blasting or scarifying methods, the high yield of such equipment and total absence of process residues enable to program maintenance interventions at best. In addition, it is possible to restore the fabric and general characteristics of a surface to “as-new” conditions at significantly lower costs than traditional resurfacing work and with far less disturbance and notably reduced operating times.
The availability on the market of a high yield machines has definitely led to new applications in the field of surface preparation and maintenance. Airport applications are numerous, both on asphalt and concrete:
- elimination of rubber deposits on landing and take-off strips
- removal of old surface markings
- cleaning oil deposits in airport parking and refueling areas
- roughening for creating anti-skid surfaces
with the advantages of effective and cost saving features:
- dry operation
- storage of residues at the same time as the operation takes place
- a self propelled vehicle which avoids the need to load and unload equipment in the zone of operation, permitting that work can be stopped and started at any time in the event of emergency
- yields of many square meters per hour
- integrity of the surface treated and the possibility of repeating the process with the same guaranty
- uniformity of the area treated
- possibility of obtaining the restoration of the macro and micro roughness at the same time as the elimination of the rubber deposits
Surface roughening work involves the restoration of safety factors in the zones where the surface, worn by traffic, no longer retains the minimum adhesion values and rainwater can no longer be drained from the surface, causing aquaplaning phenomena.
Slippery and wet surfaces are the main cause of accidents. The essential objectives to be achieved to increase adhesion are substantially three:
- the regeneration of surface roughness
- enabling the water to flow by ensuring surface draining between tyres and road surface
- ensuring dry contact between the tyre and the surface granulates by breaking down the water film
Basically two technologies are generally considered for the restoration and maintenance of asphalt and concrete surfaces:
- scarifying
- shot blasting
Scarifying is that operation featuring the passage over the surface of a machine fitted with special tools rotating on a drum. These tools, of various materials and size, are mounted in idle mode on rotating conveyor bars and graze the surface, in depth ranging from 0 to 3 mm. The tools have a larger diameter than the diameter of the flail shaft on the drum. With rotation a dynamic load is created in the cutter fails which, tending to “back away” from the centre of the drum rotation , hit against the surface to be abraded and bounce back against the shaft, producing a hammering effect. This system is particularly suitable for the recreation of the macro-fabric and at the same time creates a rough and slip proof surface. The system also allows for surface quota leveling if necessary. Such an operation can be considered economically convenient for up to 5 mm depth. In addition to rendering the surface skid proof, this action creates an ideal surface for application of products such as anti corrosion coatings, particularly on concrete roads.
Shot blasting is that procedure which employs steel micro spheres with which are bombarded, or blasted, against the surface. This impact removes the soft surface parts of the bitumen conglomerate bringing the aggregate particles into relief and thus creating macro-roughness. The aggregate, in addition to being cleaned on the surface as it is impacted without being broken, also increases in micro-roughness. Working with a high powered vacuum system, the micro spheres are recovered on the rebound, separated from the debris removed and returned into the work cycle. The dust and debris produced is extracted and stored in a special area incorporated onto the machine thus avoiding pollution of any kind. After this process, the road surface has good surface drainage performance (aggregates in relief at the water flow level) which significantly reduces the danger of aquaplaning and the projection of the water towards other vehicles in rainy conditions. At the same time, the aggregate in relief on the road surface will have taken on an irregular, jagged shape (micro-roughness) which creates greater friction with the tyres. This macro-roughness element also favours reduction of noise emission.
The availability on today’s market of machines with an operating blasting width ranging from 0.30 to 1.40 metres has led to new applications of the technology in the field of surface treatment and maintenance. By means of a shot blasting operation, it is possible to restore the fabric and general characteristics of a road surface to an “as new” condition at significantly lower costs than the traditional resurfacing work and with notably less disturbance to traffic and with reduced operating times.
Modern technology also offers scarifying machines of various widths from 20 cm to 180 cm, high production rates and all set up for dust free working if desired. Different type flails, in size and in material, guaranty minimum consumption of the road surface.